The main purpose of turbine oils is to lubricate the friction surfaces of steam and water turbines, to cool the working surfaces, and to be used as a process fluid in equipment control systems. The quality of turbine oil determines the safe-keeping and integrity of turbines as well as the reliability of their operation. The durability of turbine components and bearings specifically depends on the lubricant quality.
For a long time, turbine oils were made from petroleum. They coped with their main tasks; however, they increased the risk of fires and damage to expensive power plant equipment. In order to reduce the risk of fires in power plant turbine rooms, non-flammable or fire-resistant synthetic fluids have been used since the middle of the 20th Century. The distinctive feature of such fluilds is that they do not sustain combustion, and even if the flame arises, they do not spread in the fluid jet discharged from the equipment under pressure.
Reasons for Deteriorated Quality of Turbine Oils
During the long-term operation of turbogenerator sets, the condition of the oil fed into their lubrication systems changes considerably. This process can generally be referred to as “aging.” Turbine oil aging is characterized by oil performance deterioration.
The main causes of turbine oil aging include the following:
- Contamination with particulate matter;
- Water cutting of oil;
- Oxidation, chemical decomposition of oil with the formation of acidic products, gel and solid precipitate as a result of hydrolysis or thermal decomposition in the superheat zone on friction pairs.
The task of maintaining the quality of turbine oils at power plants is addressed by periodic purification of the oil with the use of special filtration and dehydration units that allow for removal of solid particles and water. However, these activities are sufficient only up to a certain point. For example, fire-resistant turbine oils show a sharp increase in the acid number—which is a key indicator of aging—after four years of use. An increase in the acid number during the use of turbine oil is a consequence of its instability to oxidation and hydrolysis, which both lead to the formation of acidic products. At that point, conventional filtration and dehydration units are no longer sufficient for removing such products.
In the energy sector, this task can be addressed by three methods, which are listed below:
- Adding new oil;
- Complete change of fire-resistant oil;
- Additional purification of fire-resistant oil that contains acidic compounds and aging products.
The first method of adding new oils does not really solve the problem in the long term, because acidic components and aging products quickly move into the volume of added oil, are distributed therein and induce the oil’s active aging.
The second method is used as a last resort, because a complete change of oil in a turbine is fairly expensive. In addition to the cost of purchasing new oil, financial costs include the downtime of power-generating equipment, which may last up to two weeks or even longer, the cost of remuneration for workers changing the fluid, payment for disposal of waste fluid, and purchase and disposal of flushing fluid (if necessary). The cost of changing the fire-resistant fluids will be measured in hundreds of thousands—and even millions—of dollars depending on the volume of oil contained in the turbine and the number of turbines wherein oil is changed.
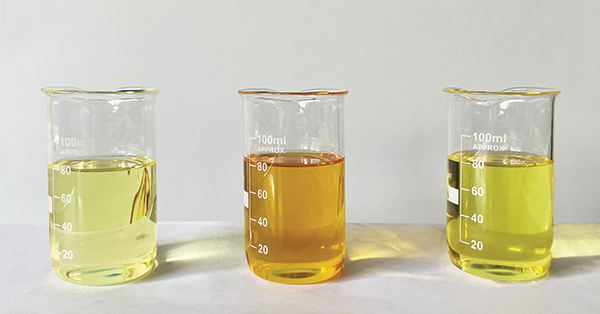
Figure 1. Fyrquel oil samples: new oil (left), waste oil before regeneration (center) and oil after regeneration (right)
Therefore, the third method with additional purification of fire-resistant turbine oils that contain acidic compounds and aging products seems to be the most practicable and feasible. In this case, we can talk about regeneration—in essence, the complete reclamation of fire-resistant turbine oil, which can be subsequently reused in power-generating equipment.
The goal of this article is to study the possibility of fire-resistant turbine oil regeneration as illustrated by the case of Fyrquel fire-resistant turbine oil with the use of Fuller’s earth sorbent.
Fyrquel is a self-extinguishing (fire-resistant) synthetic, non-aqueous fluid based on triaryl phosphate ester, which is currently used in operating the power turbines.
Results of Experimental Studies
The regeneration rate of Fyrquel fire-resistant turbine oil was evaluated by a change in acid number. The acid number of new Fyrquel oil made 0.02 milligrams of potassium hydroxide per gram. Waste Fyrquel fire-resistant oil with an acid number of 0.54 mg KOH/g was used for the experiment. Fuller’s earth was used as a sorbent for oil purification. Technically, the regeneration process was implemented with the use of a CMM-12R machine consisting of 12 sorbent-containing columns. Fyrquel oil was pumped through the sorbent columns from top to bottom once.
For a general view of samples of new oil, waste oil before regeneration, and oil after regeneration, refer to Figure 1.
Table 1. Parameters of Fyrquel Fire-Resistant Turbine Oil Before and After Regeneration with Fuller’s Earth
Number | Parameter | Before Regeneration | After Regeneration |
---|---|---|---|
1 | Acid number, mg KOH/g | 0.54 | 0.01 |
2 | Moisture content, ppm | 1,622 | 295 |
3 | Mass fraction of particulate matter, % | 0.004 | 0.004 |
4 | Kinematic viscosity at 50 °C, mm2/s | 26.67 | 27.17 |
The parameters of oil before and after regeneration are shown in Table 1.
Conclusions
Based on the study, the following conclusions can be drawn:
- The fundamental possibility to regenerate fire-resistant turbine oils has been proven as illustrated by the case of Fyrquel oil with the use of Fuller’s earth sorbent.
- The use of Fuller’s earth sorbent allows for the restoration of the acidity of waste Fyrquel oil in one pass through the regeneration machine, from 0.54 mg KOH/g to 0.01 mg KOH/g—in essence, to a value consistent with new oil.
- The use of Fuller’s earth in regeneration of waste Fyrquel oil reduced the moisture content of oil from 1,622 parts per million to 295 ppm. Yet, the particulate matter content remained the same.
- Additional studies are required for assessing the possibility to regenerate the oil with an acid number exceeding 0.54 mg KOH/g and/or the required number of passes through the regeneration machine.
The use of Fuller’s earth sorbent does not allow for the complete removal of water from Fyrquel oils, which have a high moisture content. Therefore, when regenerating the fire-resistant turbine oils with a high moisture content, it is recommended to carry out preliminary dehydration of such oils by means of special oil dehydration equipment—for example, units with coalescing filters, and only then to process the oils through regeneration machines.
Stanislav Mykytenko is a founder and director of GlobeCore, a manufacturer and vendor of industrial equipment. He can be contacted at media@globecore.com
Oleg Kryvokhyzha is a founder and director of GlobeCore. He has more than 20 years of process management experience in the field of manufacturing of equipment for power-generating plant maintenance.