Food-Grade Lubricant Regulations Ramping Up
With a growing emphasis on hygiene and safety standards throughout the food industry, particularly in recent years following the COVID-19 pandemic, food-grade greases are enjoying a continued uptick in demand.
These high-performance lubricants are specially formulated to ensure they are appropriate for use in areas where food is prepared, processed and packaged—without compromising the protection they offer machinery and equipment.
Not only do they need to defend against corrosion, friction and degradation, but they must also be non-toxic, boast excellent thermal stability and offer protection from water and steam—all while preventing any likelihood of contamination.
According to a recent report published by Global Market Insights, the food-grade lubricants segment totaled $355 million in 2022. Forecasts from the market research firm suggest that the market will grow at a 7.3% CAGR from 2023-2032.
NSF, an independent body that this year marks its 80th anniversary of helping to improve food safety standards, took the reins from the U.S. Department of Agriculture (USDA) to oversee food-grade lubricants over 20 years ago. Today, its voluntary H1 standard is recognized globally as the yardstick by which these products are measured.
H1 lubricants are those that can be used in these extremely demanding environments where there is the possibility of incidental contact with food. These are listed in NSF’s comprehensive White Book—a constantly updated online database. NSF said its H1 registrations are growing by about 6% each year.
Other categories include H2—pertaining to lubricants used in a food processing facility that should not come into contact with the food itself—and H3, often edible oils, where food contact is permitted. There is also the more comprehensive ISO 21469 certification that requires significant testing and auditing and also covers animal feed, cosmetics and pharmaceuticals.
A cautious approach is always advised when selecting the required lubricant. Foodstuffs contaminated by incorrectly specified greases may be subject to extensive and often costly recalls that can cause irreparable damage to a manufacturer’s reputation.
Of particular interest to food manufacturers and processors right now are the ongoing deliberations about mineral oil saturated hydrocarbons (MOSH) and mineral oil aromatic hydrocarbons (MOAH). The EU has long had lingering concerns about them and their potential effects on public health, calling for stronger controls.
“Even though the actual evaluation criteria for food-grade lubricants haven’t really changed in recent years, we are starting to see some changes on the horizon,” said Ismael Martinez, manager of certification for the nonfood compounds team at NSF.
“MOSH and MOAH have been on everyone’s radar for a number of years, but we’re now starting to see different regions place limits on them. Obviously, food manufacturers are looking at how to try to adjust to any new regulations and requirements. Manufacturers that are based in, or import into, Europe will likely be most affected.”
“The EU has been calling for stronger controls for MOSH and MOAH for quite some time. Although some of these limits have now been published, they have not yet really been implemented,” said Martinez. “We’re not quite there yet, but we are starting to see it get to the point where it’s ‘make or break.’ Probably later this year or early next, we’ll start hearing something more official with actual limits that manufacturers will have to follow.”
“This will be a real challenge for them as they may have to seek alternative lubricants or technologies,” he added. “Some are already making changes to their products and looking at how they can meet the new requirements. In the U.S., there isn’t the same level of concern by the FDA just yet, but they’ve been observing what’s been happening.”
Instead, polyfluoroalkyl substances (PFAS) are currently the main area of focus in the U.S., acknowledged Martinez. Known as forever chemicals, concerns remain over their potential risk and long-term effect on both human health and the environment.
With the use of PFAS by the food industry being closely examined, the entire sector is cautiously monitoring proposed restrictions that could eventually be enforced.
“PFAS has become a global issue and NSF thinks this is going to have a pretty significant impact on food manufacturers,” he said. “It’s a really hot topic for sure, with some states already limiting the amounts of PFAS in products.”
“Right now, NSF doesn’t evaluate PFAS chemicals in its H1 registration, but if the regulations do come in, then we would have to reassess this,” noted Martinez. “We’re monitoring the situation closely and looking to see how we will be able to support manufacturers in meeting these requirements to help them demonstrate that their products are PFAS free.”
The likely outcome, whenever that may be, is that food-grade greases will surely come under even greater scrutiny in the years ahead.
In this Spotlight, LANXESS discusses the performance benefits of Calcium Sulfonate Complex (CSC) grease.
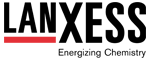
Unleashing the Power of Quality Calcium Sulfonates in CSC Grease
Market dynamics in a shifting technological landscape have provided an opportunity for an existing grease technology to take center stage. The acceptance of Calcium Sulfonate Complex (CSC) grease continues to grow unabated around the globe. This can be associated with the continued challenges, perceived and real, on lithium grease production relating to raw material cost, regulatory concerns around LiOH, and availability due to the expanding use of lithium battery technologies.
More so, it is tied to the clear performance benefits of CSC grease thickened with calcium sulfonates, versus all other thickener types. One area of continued growth is the use of CSC grease for incidental food contact applications.
What Is a Calcium Sulfonate Detergent?
Calcium sulfonate is a member of a family of chemistry better known as detergents. Detergents, specifically oil soluble detergents, have been studied and used for more than 80 years as lubricant additives with detergency and corrosion inhibition properties. These properties are useful to a wide range of lubricants and rust preventatives.
Other chemistries in the class include phenates, carboxylates (including salicylates) and phosphonates. Calcium sulfonates make up the largest portion of the additive class by volume.
The micelle structure of a calcium sulfonate is unique in that it can hold solids significantly in excess of stoichiometric balance. In one example, a calcium sulfonate easily suspends in excess of 40 wt. % solids in a stable, transparent and sediment-free liquid (Figure 1).
Figure 1.
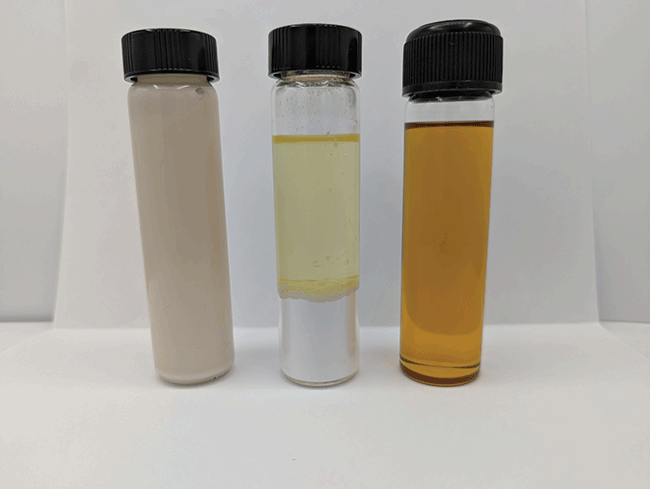
A neutral sulfonate is typically defined as having a base number (BN) less than 50 mg KOH/g. Under the right process conditions, with the right starting alkylate structure and the proper promoter, a neutral calcium sulfonate can be overbased via excess calcium hydroxide in the presence of bubbled CO2. BNs from 50 to 500 are possible.
The excess base in the micelle (Figure 2) is amorphous calcium carbonate and typically contains a small amount of free calcium hydroxide—also called free alkalinity or strong base. A sulfonate can solubilize almost half its weight of an insoluble solid (carbonate) in a final product that is bright and transparent and remains sediment free.
Figure 2.
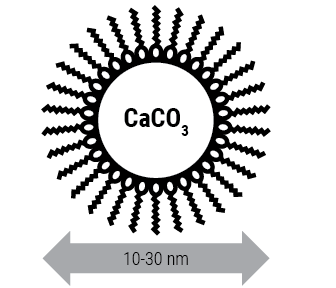
Manufacturing a Calcium Sulfonate Complex Grease
The key ingredient in a calcium sulfonate complex grease is a liquid overbased calcium sulfonate (OBCS). Selection and use of a high-quality sulfonate is a safe starting point in the manufacture of the grease.
A transportation quality OBCS is noted for its excellent performance as well as high clarity, lack of sediment and stable solubility in a wide range of oils. There is no reason to accept a lesser quality sulfonate for the consistent manufacture of a high performance and quality CSC grease.
LANXESS offers two quality overbased calcium sulfonate products: HYBASE® GF400 and HYBASE® GF500. The HYBASE® GF400 is a 400 BN overbased calcium sulfonate designed and optimized for thickening CSC grease. The HYBASE® GF500 is a 500 BN grade overbased calcium sulfonate that offers the same great performance but allows greater formulation flexibility and commercial benefits such as reduced transportation costs, lower inventory levels and additional “room” in final formulations.
An OBCS contains a large quantity of amorphous calcium carbonate. It is that amorphous carbonate that plays one of the key roles in the gelling of a sulfonate grease.
Under the right conditions, the amorphous carbonate transforms to a crystalline form, namely calcite calcium carbonate. This transformation causes the sulfonate to thicken, changing it from a Newtonian to a non-Newtonian material. Additional thickening agents and co-thickeners add to the degree of thickening, and to the stability of the thickened product. This process typically requires promoters, reagents, temperature, mixing, the addition of base oil and removal of volatile materials.
Given this complexity, there are many routes and conditions to produce a final grease, and the final properties of the grease can vary considerably.
The table (Figure 3) highlights the typical properties of a Group I CSC grease intended for industrial applications.
Figure 3. Properties of Industrial CSC Grease
Property | Method | Unit | Industrial CSC grease Group I |
---|---|---|---|
NLGI Grade | ASTM D217 | 2 | |
Color | Visual | Tan | |
Texture | Visual | Smooth | |
Dropping Point | ASTM D2265 | deg. C | 605 |
Consistency @ 60 strokes | ASTM D217 | mm/10 | 280 |
Base Oil Viscosity @ 100°C | ASTM D445 | cSt | 100 |
Mechanical Stability @ 10,000 strokes | ASTM D217 | % change | 2.3 |
Roll Stability, 50% water | ASTM D1831 | % change | 7.5 |
4-Ball EP, Weld Point | ASTM D2596 | kg | 500 |
4-Ball Wear | ASTM D2266 | mm | 0.38 |
Rust Test | ASTM D1743 | rating | Pass |
Copper Corrosion | ASTM D4048 | rating | 1b |
Wheel Bearing Leakage | ASTM D4290 | grams | 1 |
Bomb Oxidation, 1000 hours | ASTM D942 | kPa (decrease) | 55 |
Oil Separation in storage | ASTM D1742 | wt.% | 0.2 |
Water Washout at 80ºC | ASTM D1264 | wt.% (removed) | 0.5 |
Expanding the Portfolio
LANXESS has completed a project to design a new overbased sulfonate from the ground up to complement the HYBASE® GF grease feed offering in the challenging H1 Incidental Food Contact grease category.
The ever-increasing demand on performance has pushed the development of a higher tier, optimized CSC thickener feed that will fulfill tomorrow’s additional performance demands while enabling an improved H1 grease. This newly developed sulfonate is a low color, mineral oil-free, synthetic drop-in replacement thickener component for CSC grease production. It is highly soluble and produces CSC grease with excellent load and wear capacities, water resistance, corrosion resistance and mechanical stability.
In grease, the components including the base oils and thickening components are subject to compliance with 21 CFR 178.3570. The accepted chemistries are limited by the approved list both defined by the CFR and the registering bodies. It should be noted, however, that there are set limitations based on the components’ chemistry that may limit the product to a maximum treat rate in the finished grease. The limitations imposed provide a significant challenge to achieving similar performance to industrial formulated products that are not subject to registrations.
With limitations in the available componentry, food grade lubricants have historically suffered from inferior performance in comparison to their industrial equivalents, especially in the areas of corrosion, wear and extreme pressure.
A Fresh Look at Performance
HYBASE® GFX500, designed through the re-imagining of the original HYBASE® GF400, overcomes these challenges. This is a first intent, Group I base oil-free product with the target of below detection limit Mineral Oil Aromatic Hydrocarbon (MOAH) content.
This product is designed first and foremost as a grease thickening OBCS. However, other performance and product characteristic targets include:
- Transportation quality transparency;
- Ultra-low sediment;
- High stability and solubility in a wide range of oils;
- Good additive corrosion resistance; and
- Transport level detergency.
The resulting OBCS achieves all of the above targets while producing a grease with performance equal to or better than H1 CSC greases currently manufactured by LANXESS private label CSC grease processes.
In Figure 4, an industrial grade 400 BN OBCS with transportation quality solubility and transparency, HYBASE® GF400, makes an excellent performing CSC grease. Using the same CSC grease formulation, an un-optimized synthetic HX-1 formulation makes a lighter grease. However, the sulfonate itself does not have quite the same transparency as the HYBASE® GF400.
Figure 4.

After comparing the sulfonate structure in the first two, HYBASE® GFX500 was designed from first intention with the goal of optimal solubility, clarity, grease thickening and detergency. These core features resulted in equal or greater results in grease performance while resulting in a light, transparent OBCS and low color grease.
Calcium sulfonate complex grease continues to capture market share especially in the food processing industry. This grease technology needs to continually improve to keep up with changing regulatory and grease user demands.
LANXESS has identified that those improvements need to start with the re-design of the OBCS used to thicken the grease—and has been working on just such an OBCS for the past few years.
A newly designed and optimized, high performance, mineral oil-free OBCS has been developed for thickening H-1 quality CSC grease. Hybase GFX500 is a next generation HX-1 quality OBCS with high clarity, synthetic calcium sulfonate, which will produce a low color, high performance H-1 CSC grease.
To find out more about Hybase calcium sulfonate detergents, visit https://lanxess.com/en/Products-and-Brands/Brands/Hybase