A tribological coating allows for increased production of vaccine vials.
For the past year, pharmacologists around the world have raced to develop new COVID-19 vaccines that open a path to recovery from the economic damage caused by the virus, if not from loss of life.
From this extraordinary mobilization of people and resources have come 13 approved vaccines, with scores more in trials. Health authorities are now administering these drugs to as many people as possible in the shortest reasonable amount of time. To do that requires billions of doses, each contained in tiny glass vials.
The borosilicate glass from which most of these vials have been made for more than a century could be standing in the way of faster deployment.
Borosilicate glass was invented in 1897 by Friedrich Otto Schott, who lent his name to one of a few companies worldwide that today make glass vials for parenteral medication—or medicine not administered orally.
This high-melting point glass is made from a mixture of 80% silica and 10% boric oxide, with a few other ingredients making up the rest. Its resistance to thermal shock makes it a good material for lighting, optics, laboratory flasks and cookware.
It is on the fast-moving, ultra-sterile pharmaceutical filling lines where its shortcomings come to the forefront, and they can be expensive and dangerous.
Borosilicate vials are molded from red-hot glass tubes, but the high temperature can make volatile boron leech out and weaken the vial. If this occurs inside the vial, these weaker areas can react with the contents until use, causing delamination—a mode of failure in which a material fractures into layers—of glass flakes into the solution. This is clearly a hazard to patient safety.
During filling, freeze-drying the contents to remove unwanted water places additional stress on glass vials, as the frozen liquid can expand by as much as 10%. Some COVID-19 vaccines that use messenger RNA, such as Pfizer-BioNTech and Moderna, must be stored at around minus 80 degrees Celsius.
“A lot of these new vaccines based on messenger RNA … require deep-freeze storage, and glass is not the best for that,” Chris Weikart, chief scientist at SiO2 Materials Science, a pharmaceutical packaging company based in Auburn, Alabama, told Lubes’n’Greases.
The production process also subjects the vials to friction as they race through high-speed filling lines. Glass feels smooth to the touch, but when magnified it is a landscape of ridges and valleys that account for its fragility. It is even possible to strike a match on a window.
As the vials rub together, they create glass dust that can contaminate the contents and the surrounding workplace. They also produce lots of noise, which can be a health and safety hazard for people nearby.

Combined, these make borosilicate vials prone to cracks and breakages, which would render batches of crucial vaccine useless, while also slowing production—something that can be ill afforded during this time of pandemic crisis.
“Glass usage in pharmaceutical applications is tricky, as a clear breakage of glass is of obvious safety concern to patients, etc. But a non-catastrophic glass breakage is of concern to the sterility of the product,” said Raj Shah, a fellow of the Society of Tribologists and Lubrication Engineers and director of Koehler Instrument Co. in Holtsville, New York.
Pharmaceutical packing therefore uses glass that is thermally or chemically tempered to improve its mechanical properties and durability. This works well for flat geometries, but for complex shapes such as vials, thermal tempering is tricky. Chemical tempering helps strengthen the glass from blunt impacts, but it is still prone to scratching and mishandling that may happen during manufacturing, Shah explained.
“There is a definite need to have alternative solutions, and a low-friction coating would help solve some of these issues,” he said.
A Call for New Materials
In 2011, the United States Food and Drug Administration issued a letter of caution to pharmaceutical manufacturers of the risks posed by delamination and called for the development of new vial material.
Since then, two companies have developed solutions to this century-old problem, both of which use alternative materials with a coating.
Corning Inc., a specialty glass company headquartered in New York, developed a new glass vial it believes is the ideal and timely replacement for borosilicate, able to satisfy the new demands of rapid mass vaccine production.
In response to complaints from pharmaceutical companies that borosilicate lacked sufficient mechanical strength, the research and development team tried more than 200 glass compositions before choosing aluminosilicate.
Corning says the aluminum, as well as calcium and magnesium, increases the vial’s strength by up to 10 times over borosilicate, so much so that a vial survived being dropped down a three-story stairwell by a customer to test the product’s robustness. Aluminosilicate glass can also withstand temperatures up to 800 ˚C, whereas borosilicate can tolerate 500 ˚C before it begins to soften.
The vials are further strengthened by submerging them in a salt bath to replace sodium ions in the glass with larger potassium ions.
The result is Valor Glass, introduced in 2017 in collaboration with pharmaceutical companies Merck and Pfizer.
Not by Glass Alone
What makes Valor Glass vials interesting for tribologists is their coating. While Corning declined to share specific technical details of the coating with Lubes’n’Greases, it did say that it is a “low coefficient of friction coating that improves manufacturing speed and efficiency for the vials on filling lines.” In a patent application filed in 2018, the coating is described as a coupling agent and a polyimide film. Polyimides are a class of high-performance plastics prized for their strength, flexibility, thermal stability and chemical resistance.
Vials can pile up before going through narrow tracks in filling machines, forming a bottleneck similar to grains of sand in an hourglass or grain silo, explained Mathias Woydt, the managing director of German lubrication and technology development company Matrilub in Berlin.
This is caused by high friction between individual grains or in this case between vials. Minimizing this force, measured as the coefficient of friction, prevents pile-ups and speeds up the throughput rate.
The coating reduces friction, allowing vials to more easily—and quietly—slide past each other. It also helps improve product durability, enabling the glass to withstand exposure to higher temperatures, some of which are experienced during manufacturing and packaging processes, Shah explained.
“Such a low-friction coating definitely serves a much needed role in helping to make a safer product to manufacture, use and transport without undue damage,” Shah said.
The patent also indicates that the coating has a coefficient of friction of up to 0.2. The coefficient of friction places a numerical value on the amount of friction between two surfaces. The lower the value, the less force is required for sliding to occur. Although the coated glass has a coefficient of friction that is not as low as, for example, lubricated polished metal surfaces, it is half that of uncoated glass, Woydt said.
Woydt also noted that the coating must be able to withstand being sterilized with hot air and steam at high temperatures. Valor’s coating can withstand temperatures between minus 180˚C and 400˚C. A polytetrafluoroethylene coating, for example, would not fare as well, he explained.
Corning claims Valor’s tougher structural properties and the coating combine to increase filling machine throughput by up to 50% more than borosilicate vials.
Plastic Fantastic
SiO2 Materials Science took a different approach and has avoided glass vials altogether. Instead, its vial is made from a medical-grade polymer sourced from Japan. The vial is also crafted with an interior layer of silicon dioxide thinner than a human hair.
“We actually put a coating on the inside of the vial, and that’s purposely done to improve the barrier properties. You don’t want anything from the polymer or the environment getting into the drug product,” Weikart said.
Using polymer has several advantages over glass. It is more stable at the subzero temperatures required to store some medications, including the COVID-19 vaccine made by Moderna, which is a buyer of the SiO2 vial. It does not delaminate and shed particulates into the solution. It is significantly stronger, which reduces the risk of breakages during the manufacturing, filling and transportation processes.
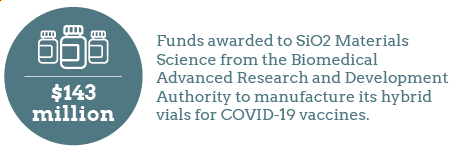
“Every glass breaks. There may be tougher versions of it, but just take your cell phone [as an example]. I can’t tell you how many times I broke my Gorilla Glass screen protector,” Weikart said. Corning is the inventor of Gorilla Glass.
Crucially, friction on the production line is not an issue for SiO2’s polymer vials. Because of this—aided by three additional production sites and 491 new employees—production of these vials has increased from 10 million units per year to that number per month.
“Our polymer vial probably has a lower coefficient of friction than most plastics. The only exception would be Teflon,” Weikart said. “We’ve never had any problems running our vials through a standard fill-finish line, purely from a friction point of view. It hasn’t been an issue that we’ve had to find a solution to.”
Simon Johns is an editor with Lubes’n’Greases. Contact him at Simon@LubesnGreases.com.